No matter what you do, it is essential that the devices you use take accurate measurements. From weather to the medical field, automotive to agriculture, from local to global business, and more, one fact remains the same. Precise measurements are essential to making decisions and performing tasks.
You might be thinking that your equipment was built to be rugged and checked when it comes off the production line, so there is no need to make sure that it still works the same, but that is not the case.
Proper calibration matters. This article will explain why.
What is calibration?
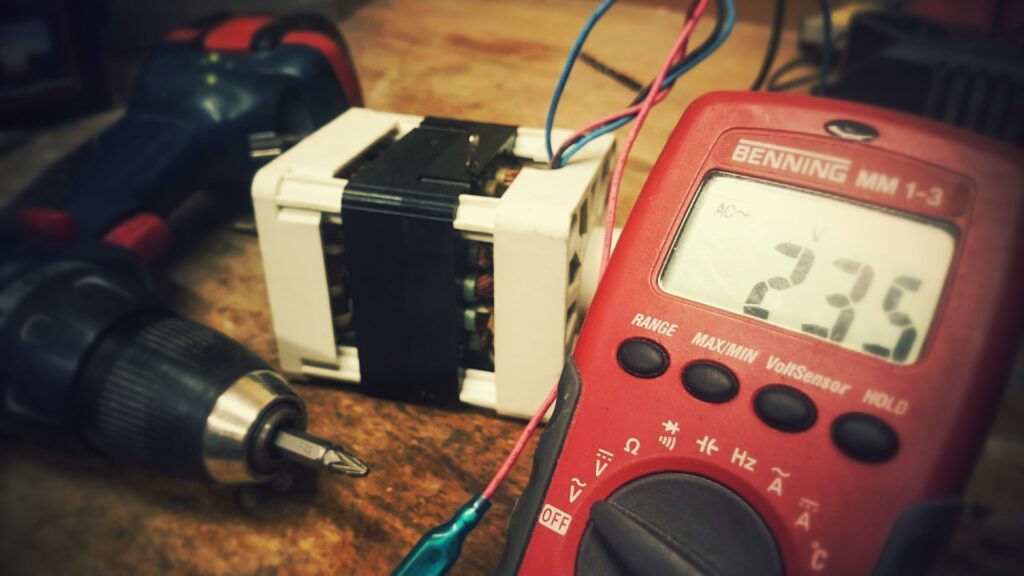
Calibration is the process of configuring an instrument to ensure it provides an accurate measurement. It is an essential routine necessary to maintain equipment, save time, money and provide reliable results. While many factors could influence a measurement device, such as environment or user error, ruling out a misaligned calibration is a significant first step in problem-solving.
It is a procedure where you compare a Device Under Test (DUT) with an unknown value with a known value’s reference standard. Through this, you can look out for any errors to further correct the device for accurate results.
Mostly, a calibration process is carried out when the machine or tool is new. As it just came in from the manufacturer, there are high chances of it not showing perfect results. Calibration helps in correcting the machine so that no errors are found in its measurement values.
Why you should calibrate your instruments
The calibration of instruments is all about confidence in the measurement results you’re getting. Calibrating your device assures you that your measurements are accurate within the specification limits that led you to select the instrument in the first place. Routine calibrations are your prescription for the continued health and performance of your appliance.
Calibration is vitally important wherever measurements are essential. It enables users and businesses to have confidence in the results they monitor, record, and subsequently control.
The accuracy of measuring instruments degrades over time, but regular calibration is the best way of minimizing this degradation and maintaining the accuracy of your equipment. The more accurate a product, the more time and money you save with measurements that you can depend upon.
An uncalibrated instrument will be costlier in the long run. As unforeseen costs of inaccurate measurements can quickly skyrocket. Here are some benefits of having your equipment adequately calibrated:
Improved product safety
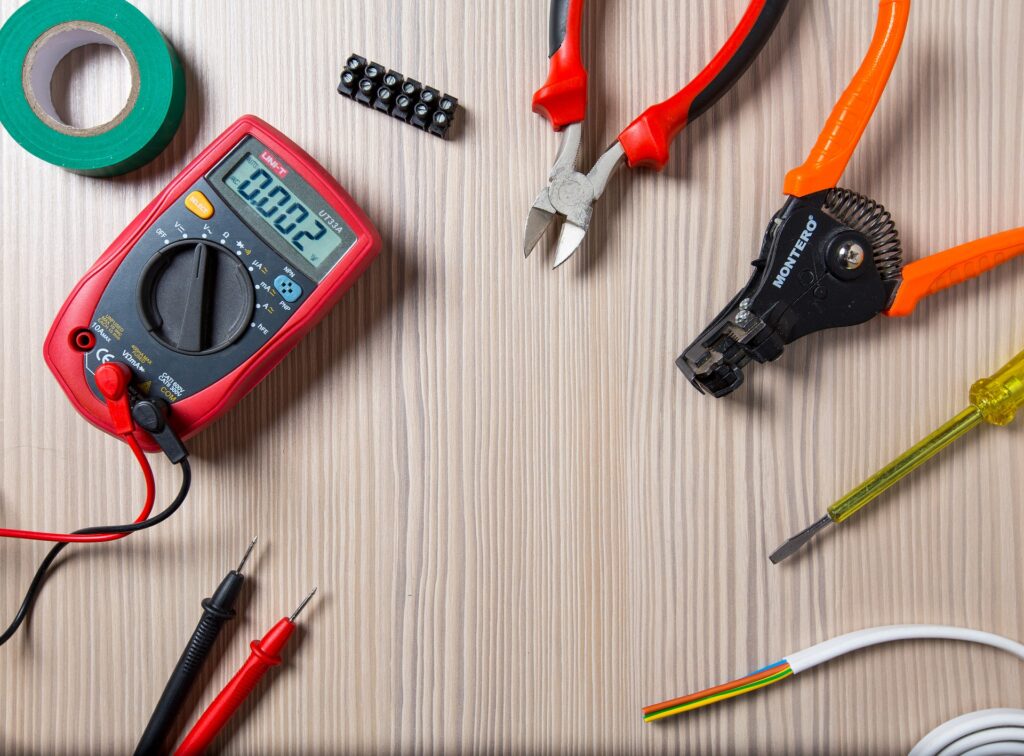
When measuring any parameter, it is crucial that the quantity measurement is accurate to maintain product safety. For example, if you measure a force or electric current, it could pose a safety hazard if it is not correct.
If a vehicle’s component were to fail at a specific measured pressure, but that measurement was performed with an instrument that was not calibrated to ensure accuracy, an accurate failure analysis couldn’t be completed.
In a science lab that works with volatile chemicals, small changes in numbers can quickly put your staff in danger.
Greater reliability
You might have the most sophisticated and costly instruments, but your results will have no significance if you do not calibrate them periodically.
Even low-cost instruments such as thermometers, pH meters, volumetric apparatus, and ovens need to be calibrated from time to time to give reliable data.
Items like weights, measurement rods, volumetric apparatus that do not seem to change with time also need to be calibrated against reference standards not just at the time of purchase but regularly at defined intervals.
The need for such calibration arises due to changes in environmental conditions such as temperature, humidity, and improper handling, leading to wear and tear.
Instrument calibration is always against a traceable standard which is maintained under specified environmental conditions. Traceability to known national and international standardization bodies such as ISO, NIST, ASTM, BIS, BS, AOAC, etc., is necessary.
Fewer errors mean lower costs
In manufacturing, a production process resulting in defects can be very costly. Small measurement errors can cause a part to set improperly and be faulty. The process would need to stop, restart, and have parts remade. This is expensive both in time and resources, or worse, the defective parts could get to the customers.
To help reduce the potential for manufacturing defects, the sensors monitoring these processes should be accurate. Calibrating gauges and instrumentation will minimize the possibility of production defects.
When should you calibrate your instruments?
Always check the manufacturer’s recommendations for guidelines on when best to calibrate individual instruments. Outside of that, regular and periodic checks should be done either annually, quarterly, or even monthly. Recorded and regular checkups will ensure devices are as accurate and reliable as possible.
Consider the cost of calibration as an investment and the possible results of an incorrect reading as the cost of not investing.
For most industries, the standard is to calibrate annually. As you gain results from calibration tests, you will be in a position to adjust the frequency of calibrations potentially or upgrade to more robust measuring instruments if needed. Most calibration laboratories supply a printed calibration certificate for the customer to retain as proof of quality standards.
Calibration is necessary when an instrument is relocated even within the same laboratory, after a major repair, or even if a new accessory is installed.
You should not worry about the cost associated with calibration because it is minimal compared to the importance of calibration. As calibrated equipment will show more accurate results, you can easily cut out on further costs of making errors with this process. So it is more of an investment than an item of expenditure, and you must carry it out at specific intervals.
Conclusion
Calibration is essential because it helps ensure accurate measurements. Precise measurements are foundational to the quality, safety, and innovation of most products and services we use and rely on every day.
Calibration brings the assurance of precise measurements required in research, development, and innovation, and the production of millions of products and services worldwide. Exact measurements are critical to the comfort, quality, and safety of products and innovation we enjoy and rely on every day.
Check out our garden ideas as well.